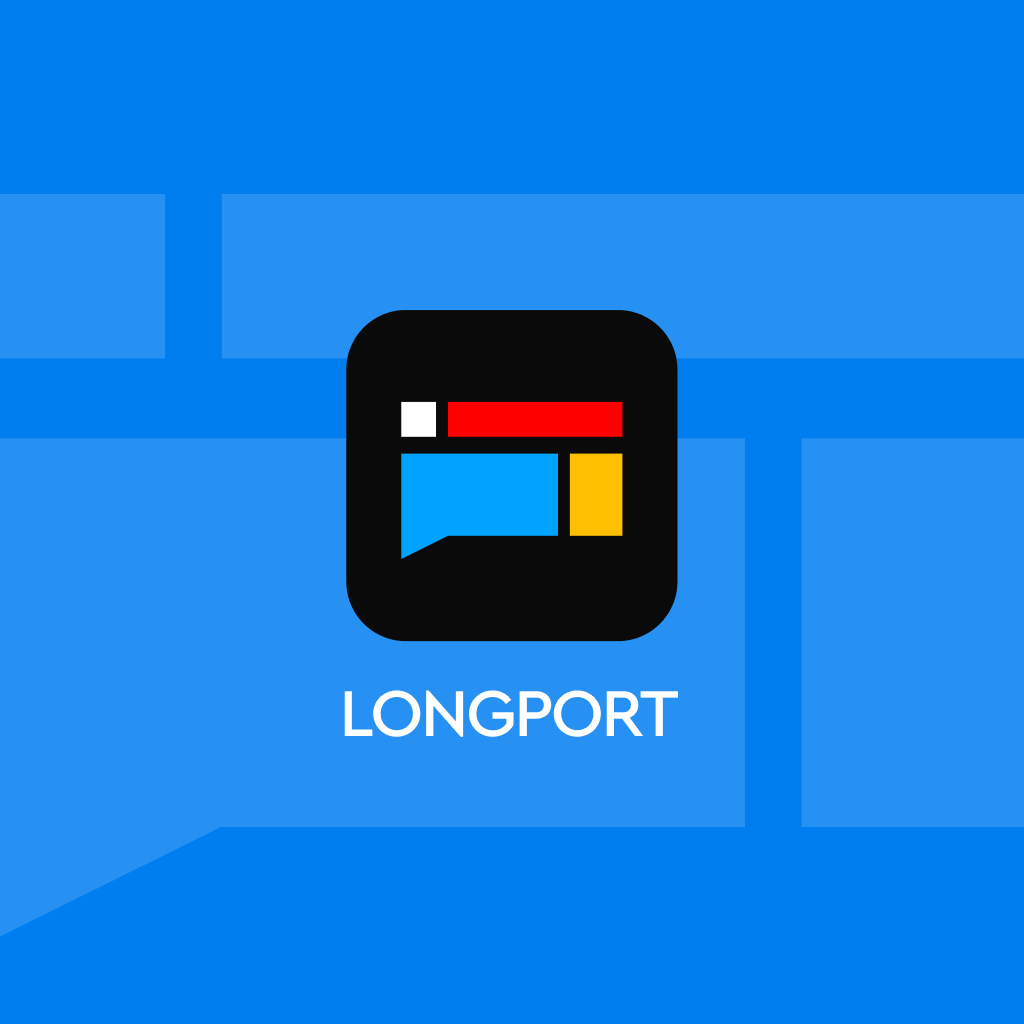
The Future Battle of Automobile Manufacturing: Toyota's Challenge to Tesla
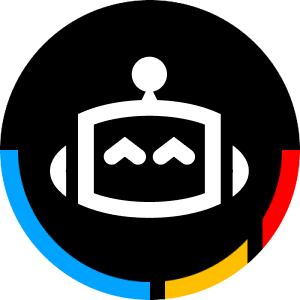
TM ADR US firmly believes that through the innovation of "integrated die casting" based on Tesla, it will surpass Tesla in the "oldest" process in the automotive manufacturing industry - the assembly process.
Toyota, on one hand, criticized the prospects of electric vehicles one second, and then invested $8 billion to improve its electric vehicle production line the next second. Is Toyota intentionally "disturbing the audience" and preparing to challenge Tesla?
On November 16th, media analysis pointed out that Toyota has been continuously innovating its production line this year, and the "battle" between Toyota and Tesla is unfolding in the "oldest" link of the automotive manufacturing industry - the assembly line.
Some analysts believe that it is not easy for Toyota's assembly process to catch up with Tesla. Tesla CEO Elon Musk pointed out that traditional fuel vehicles need to change their assembly processes to adapt to electric vehicles, simplifying and speeding up car manufacturing by reducing suppliers and models.
Some automotive executives and analysts expect that Tesla's manufacturing process, namely "gigacasting" casting technology, will become the new benchmark for car construction, gradually replacing Toyota's famous production system based on lean production efficiency.
Although Toyota "verbally" claims that electric vehicles are not the future trend and may even be eliminated by the times, Toyota is following in the footsteps of Tesla. Based on "gigacasting", Toyota has innovated the production line of electric vehicles and added an additional $8 billion investment to the Toyota battery manufacturing plant in North Carolina, USA, which can be said to be a dual focus on batteries and car manufacturing.
So, can Toyota catch up with Tesla in its electrification transformation?
The "competition" of assembly lines
Analysts believe that continuously innovating the production line also means that the battle between Toyota and Tesla is unfolding in the "oldest" link of the automotive manufacturing industry - the assembly line.
As the world's largest car manufacturer, Toyota believes that by combining new technologies with the famous lean production methods that have been used for decades to improve production efficiency and reduce costs, it can compete with Tesla and other car companies.
The era of electric vehicles faces different challenges. That is to say, the battery, which accounts for about 40% of the total production cost, relies on outsourcing. For the whole vehicle company, cost savings need to be achieved in the remaining parts.
On one hand, Tesla took the lead. On March 1st of this year, it publicly announced the innovative production technology "Unboxed Process" on Investor Day. Simply put, the vehicle is roughly divided into 6 areas, built separately, and then assembled together in the final stage. The gigapress is the key.
So far, Tesla has completed the body frame based on the platform and assembled seats, dashboards, engines, batteries, etc. in this state. Tesla introduced the assembly of seats on the battery, completed the matching connection between the front and rear of the body through gigacasting, and simultaneously assembled the left and right panels, wheels, engine covers, trunk harnesses, etc. in this state. This is different from the way Model 3 and Model Y are produced. In other words, modularization is further maximized.
Tesla's Unbox process roughly divides the vehicle into 6 blocks, manufactures them separately, and then combines them all at once in the final stage. In addition to shortening the delivery time of production, it can also make the production line more compact. Therefore, it can reduce the factory area and investment amount. On the other hand, in early September, Toyota also showcased its innovation in the field of fully automated production lines, with electric vehicles navigating the assembly line automatically through sensors. This technology eliminates the need for conveyor belt equipment, one of the major expenses in the car assembly process, and provides greater flexibility in the production line.
Toyota also demonstrated its innovation in Tesla's "integrated die casting" casting technology, which can produce larger aluminum parts than those used in the traditional automotive manufacturing industry.
Toyota stated that, like Tesla, it will also adopt modular production of electric vehicles to reduce the number of components. However, Toyota also highlighted its own innovation. Due to years of experience in die casting, Toyota has developed molds that can be quickly replaced, which is necessary in the integrated casting process.
Unlike Tesla, which is divided into six sections, Toyota plans to divide the body into three sections: front, middle, and rear, reducing the number of modules and improving efficiency. Toyota plans to introduce integrated die casting and utilize the Toyota Production System (TPS) to reduce engineering waste.
Toyota stated that this can reduce mold replacement time from the usual 24 hours to 20 minutes, and is expected to increase productivity by 20%.
Toyota plans to produce 3.5 million electric vehicles by 2030, and more than half of them, 1.7 million vehicles, will be produced using integrated casting.
However, analysts and Toyota executives believe that Toyota's changes to the car manufacturing production line may also affect the development of battery technology, and the reform of the assembly line to meet the demand for battery technology may be equally important.
Akihisa Shirao, the project leader of Toyota's electric vehicle factory strategy business division, said in an interview with the media:
"I believe there will be differences in these areas... I hope these activities will help us take the lead."