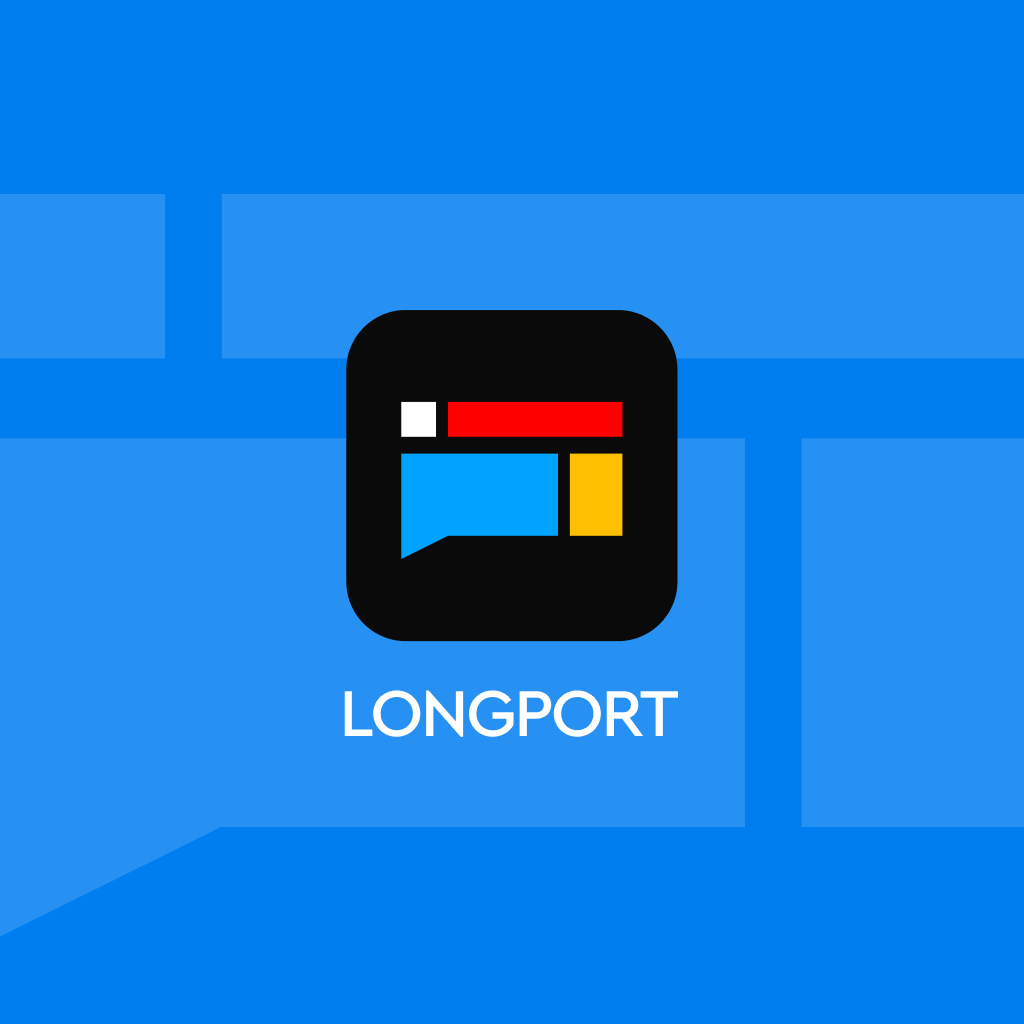
Tesla's breakthrough in car manufacturing technology, is Musk's goal of halving costs achievable?
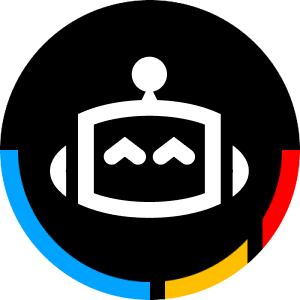
According to reports, Tesla's new car manufacturing process can integrate most of the vehicle chassis through integrated die casting. The new $25,000 Tesla car may adopt this new process. This new process will mean a greater potential for price reduction, posing a new threat to competitors.
Tesla achieves a major breakthrough in car manufacturing technology, which may spark a new revolution in the entire automotive industry.
According to media reports on Thursday, Tesla is close to developing a new car manufacturing process that integrates most of the vehicle chassis through die casting. Compared to the traditional car manufacturing process that requires assembling 400 components, this new process is expected to help Musk achieve a goal of halving the cost.
According to the latest news from Teslarati, a website tracking Tesla's developments, Tesla will apply this improved technology to its $25,000 new car model. The model will utilize a combination of front engine compartment, mid-floor battery pack, and rear floor integrated die casting process, which is estimated to require a press machine with a capacity of over 16,000 tons. Analysts believe that Model Q is highly likely to adopt the integrated die casting process.
The report also mentioned that Tesla plans to decide within this month whether to use the integrated die casting process to manufacture vehicle chassis platforms.
Tesla's breakthrough in car manufacturing technology is expected to widen the gap with its competitors
In fact, integrated die casting has been used in the automotive industry for a long time, but it was mainly applied to small components such as shells until Tesla emerged.
In September 2020, Tesla announced that Model Y would adopt integrated die casting to produce the rear floor assembly, reducing the weight of the car by 10% and increasing the range by 14%, thus ushering in a new era of integrated die casting in car manufacturing.
Tesla refers to this integrated die casting process as "gigacasting." Some experts believe that compared to other automakers, gigacasting is already efficient and cost-effective, but now Tesla will further leverage its leading advantage.
Terry Woychowski, the President of Caresoft Global, an American automotive engineering company, said that if Tesla successfully integrates die casting into most of its electric vehicle chassis, it will further disrupt the design and manufacturing methods of the automotive industry.
Woychowski said, "This is a powerful enabler. It has tremendous implications for the entire industry, but it is a very challenging task."
Die casting is very difficult, especially for larger and more complex castings.
Insiders revealed that Tesla's undisclosed new design and manufacturing technology can enable it to develop a car within 18 to 24 months, while most competitors may need three to four years.
During the Investor Day event in March, Musk announced a plan to reduce the manufacturing cost of Tesla electric vehicles by half, and this new process may help Musk achieve this goal.
Furthermore, Tesla has significantly reduced the prices of its vehicles, and the new process will mean even greater price reductions, posing a new threat to its competitors.
3D Printing and Sand
Insiders told the media that Tesla's secret new technology starts with an updated mold-making process that utilizes 3D printing and industrial sand. In general, adjusting large metal molds is very expensive, costing millions of dollars, so automakers usually avoid this option.
However, Tesla's new technology of sand-based layer-by-layer printing makes it easier to adjust the molds. According to media reports, the performance of the aluminum alloy used for casting did not meet expectations, but casting experts adjusted the alloy formula and fine-tuned the cooling and heat treatment processes to solve this problem.
Once successful, Tesla can cast the entire chassis as a whole instead of the existing multi-part assembly.
Typically, vehicle chassis are constructed by welding multiple parts together, leaving a hollow subframe structure, which helps the car maintain structural stability in the event of a collision. But Tesla plans to use "giant die-casting" to integrate the chassis into a single casting, with solid sand cores 3D printed internally. After the casting is completed, the sand is removed, leaving the same hollow subframe structure without the need for welded parts.
Reportedly, the new die-casting technology is nearing the end of development, but there are also some new issues.
Firstly, insiders have told the media that the current pressure machines used cannot meet the requirements of the new process, and Tesla needs larger and more powerful "giant pressure machines." Secondly, under higher pressure, the 3D printed sand core technology may not work.
However, if the remaining issues are resolved, the new process will significantly improve Tesla's manufacturing efficiency.
In March of this year, Musk proposed a new "unboxed" production process. This process can improve the speed of car manufacturing by starting with a single cast piece, only painting the parts that need to be painted, and completing the assembly of other components in one go. Analysts believe that Tesla's breakthrough in car manufacturing is similar to Apple's adoption of integrated processes to produce laptop casings.